The Role of Milking Equipment in Mastitis
By G.M. Jones, Professor of Dairy Science and Extension Dairy Scientist, Milk Quality & Milking Management, Virginia Tech.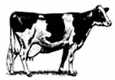
Introduction
Cow Handling and Preparation
Desired Characteristics fo a Milking System
Relationship Between Milking Equipment and Development of Mastitis
Sources of Vacuum Drops from Vacuum Pump to Teat End
Frequency of Slipping or Falling Teatcups
Milking System Performance Analysis
Preventive Machine Maintenance
References
Introduction
The goal for any dairy farm should be to deliver a high quality product that has consumer appeal. The objective of any heards milk management program should include:(a) maximise yield secreted by the mamary gland,
(b) milk cows out in a short peroid of time,
(c) prevent damage to teats, teat ends, and the udder, and
(d) have no adverse effect on chemical composition of milk.
It must be recognized that factors other than milking equipment, such as milking practices, can influence milking performance and quality.
Cow Handling and Preparation
Milk yields and milkability are maximized when calm cows are milked with a consistent routine at every milking. Proper cow handling and udder preparation will decrease unit on-time. Routines should be consistent from one milking to the next and from one milker to the next. A minimum of 12-15 seconds of teat contact time is required for sufficient nerve stimulation to ensure adequate oxytocin release and a good milk ejection response (Mein and Reid, 1996). Units should be attached within a window of 60 to 90 seconds from beginning of udder preparation process to take advantage of oxytocin stimulated by good teat manipulation.Desired Characteristics of a Milking System
1. Provide good milking performance. Cows should milk out cleanly and in a short period of time. The milking system should not interfere with milk let-down, which could reduce yield and alter composition. Many years ago, research showed that mastitis in subclinically infected cows became clinical when cows were not milked out.2. Prevent contamination of teat and udder tissue with increased bacteria concentrations that invade and infect the udder, causing development of new mastitis infections and higher somatic cell counts. Bacterial invasion of the teat can result from: (a) transfer of infectious organisms from cow to cow on teatcup liners, (b) cross contamination from one quarter to another on the same cow caused by pressure changes within the milking unit, (c) conditions that damage teat ends and allow organisms to colonize and multiply in damaged tissue, and (d) conditions that create teat end impacts by bacteria-laden milk droplets with sufficient velocity to enhance the ability of mastitis-causing organisms to enter the teat canal and access the udder.
3. Provide adequate collapse of teat cup liners and massage of teats during the pulsation cycle. The function of pulsation is to massage the teat at regular intervals and maintain blood circulation, preventing teat congestion. Malfunctioning pulsators and/or poor teatcup liner performance may lead to inadequate milk removal and/or damage to teat ends, causing mastitis and reduced milk production (Bray et al., 1998).
4. Be easy to clean, handle, and maintain.
Relationship Between Milking Equipment and Development of Mastitis
The teat canal is the primary defense against bacterial invasion of the udder. The teat canal is lined with a keratin layer which plays an important role in preventing infections. The keratin layer can be removed by overmilking, high vacuum levels, and hard liner squeezes which increase infection rates, especially with higher production.Milking machines may adversely affect udder health by damaging or changing the resistance of the cow’s first line of defense: teat skin, teat canal, and mucosal tissue. As the teatcup liner opens, a reverse pressure gradient can be created across the teat canal that causes bacteria-contaminated milk droplets or slugs of milk to move backward and impact against the teat end. Bacteria or bacteria-contaminated milk droplets present at the time penetrate the teat canal and enter the teat. These impacts are caused by air admission into teat cups or claws (liner slips). The frequency of impacts increases with sudden large air admission into the cluster due to liner slips (enhanced by wet cow milking), improper application or removal of teat cups, vigorous machine stripping, and inadequate positioning of the milking unit under the cow. Milk droplet impacts can be minimized by: avoiding abrupt vacuum loss through adequate reserve air flow, proper milk line sizes, sensitive vacuum regulation, proper unit application and removal, and adequate air flow into the claw vent.
According to the National Mastitis Council (1996), there are four ways in which the milking machine can be involved with the development of mastitis.
1. Facilitate the transmission of pathogenic bacteria between cows or quarters at milking time. The milking process offers multiple opportunities for bacteria to be transferred between cows and quarters. Cross infections may account for as much as 40% of new infections. Improper udder preparation, such as using a common towel or failing to dry teats, increases contamination and transmission of bacteria. During milking, vacuum fluctuations in the unit claw result in milk moving between teat cups. If the cow being milked has one or more infected quarters, this process transfers pathogenic bacteria to the surfaces of other teats. Also, after an infected cow has been milked, contaminated milking machine liner surfaces carry bacteria originating from the teat surface and milk of that infected animal to the next animal when the machine is applied.
2. Aid the multiplication of bacteria at the teat end. The major factor influencing new intramammary infection is exposure of the teat orifice and duct to pathogenic organisms. Machine milking can influence teat end contamination by modifying conditions at the teat end so that bacterial colonization occurs more readily. These conditions are often referred to as teat orifice "eversion," or "hyperkeratosis" where the teat canal looks like it is being pulled inside out. The development of lesions. hemorrhagic blisters on teat ends, and teat chapping has been associated with improperly operating milking machines. Such skin abnormalities are readily colonized by pathogenic bacteria, and may lead to intramammary infections.
3. Increase bacterial penetration of the teat duct. Abrupt reduction in milking vacuum can cause backward movement of air toward the teat end, propelling droplets of milk containing bacteria directly from the exterior of the teat into the teat sinus. This "impact mechanism" results from vacuum fluctuations. Liner slip is an important event in the generation of vacuum fluctuations. The impact mechanism is the only known means by which vacuum fluctuations are capable of increasing infection rate under both experimental and field conditions.
4. Modify the teat or intramammary environment to enhance bacterial infection or impair host defenses. Machine milking may cause trauma to the teat rendering it more susceptible to colonization and infection. Trauma to the mucous membranes lining the teat sinus may provide an environment favoring bacterial colonization or multiplication. Local pain may lead to neurohormonal responses which suppress immune function and increase the likelihood of disease as well as interfering with milk ejection or "letdown."
A vacuum pump creates the vacuum inside the teatcup liner by removing air in the system of pipes and hoses between the pump and the liner interior. The vacuum level at the teat-end depends on the degree of vacuum drop introduced by each component in the path from the pump to the teat end. The teat end vacuum should be at a level and degree of stability compatible with rapid, complete milk extraction and minimal tissue trauma. Both experimental and field experience have shown that a vacuum level of 10.5-12.5 inches at the teat end during peak milk flow offers the best combination of rapid, complete milk removal with minimal physical harm and highest milk quality (Stewart et al., 1996).
Nominal system vacuum settings of 12.5-13.5 inches for low lines, or 14-15 inches for high lines, will result in a vacuum level in the claw within 10.5-12.5 inches during peak milk flow. Lower values may result from excessive milk line height, restrictions in the milk tubes, excessive vacuum drop across ancillary components, blocked air vents, excessive air admission through air vents, or air leaks into the cluster. Claw vacuum during peak milk flow should be about 12-12.5 inches to milk cows as quickly as possible but still maintain gentle milking conditions. An average vacuum fluctuation of less than about 2 inches is considered desirable for a low line system and less than about 3 inches for a high line system. Higher vacuum fluctuations may indicate either a blocked air vent or excessive air flowrate through air vents or air leaks. Increasing the system vacuum level, e.g., from 13.5 to 15 inches, results in faster milking time which may be offset by higher strip yields, higher incidence of hyperkeratosis at the teat orifice, and more machine-induced teat congestion and edema, unless cow preparation procedures are excellent.
Vacuum drops occur for several reasons, including admission of air intentionally or unintentionally into the system, friction in plumbing when moving air, solid slugs of milk being conveyed in the milk pipeline, friction in long milk hoses when moving an air and milk mixture, and expenditure of energy to overcome gravity when lifting milk (Table 1). The sources of these drops need to be identified to maintain teat end vacuum in the desired range while operating the pump at the most energy efficient and power efficient (i.e., lowest) vacuum level. Table 1 probably should include faulty vacuum regulators or vacuum pumps but it does not.
Table 1. Sources of Vacuum Drops from Vacuum Pump to Teat End (Stewart et al., 1996) | |||||
Steady leakage of air due to unplanned air admission | Sporadic leakage of air due to unplanned air admission | ||||
Cracks in lines, at pipe fittings, pulsator ports | Unit fall-offs | ||||
Holes in the distribution tank | Liner slips | ||||
Leaks at milk line inlets and other claw-to-milk line locations | Air admission with unit removal or unit applications | ||||
Cracks in claw bowl or leaks in claw shut-offs, holes in liners or hoses |
Since environmental bacteria usually do not colonize the teat canal, an active force is needed in order for these bacteria to penetrate the canal (Rasmussen et al., 1994). Proper premilking teat preparation lowers the number of bacteria at the teat end before attachment of the milking unit. Some bacteria pass through the teat canal during milking. The risk of reverse pressure gradients can be lowered by milking well-prepared cows who let their milk down before attachment of the milking unit and properly removing the unit as soon as cows are milked out.
Frequency of Slipping or Falling Teatcups
A problem exists if more than 5-10 slips or fall-offs per 100 cow-milkings require correction by the milker. Slipping or falling off early during the milking process often result from low vacuum level, blocked air vents, or restrictions in the short milk tube. Slips occurring during late milking can be due to poor cluster alignment, poor liner condition, or uneven weight distribution in the cluster (Mein and Reid, 1996).Unit Attachment. Prior to attachment, the short milk tubes should be bent over the claw ferrule to prevent air leakage into the claw. As individual teatcups are attached, the teatcup assembly is raised up toward the teat and the stem of the liner straightened out to minimize air admission into the system. Reverse pressure gradients during attachment were reduced when milk ejection (let-down) had occurred before attachment (Rasmussen et al., 1994).
Unit Alignment and Support. The outlet of the claw should point in a slightly downward direction directly at the head of the cow in most conventional systems or directly out between the legs in a parallel parlor. Proper unit adjustment will minimize liner squawks, especially toward the end of milking. Frequently, the milk hose and long pulse tubes pull and twist the claw so that the cluster does not hang evenly, thereby causing uneven milkout and increasing the number of liner squawks. The use of simple mechanical devices help to align the unit squarely on the udder. Randall arms need to be long enough to position the claw outlet parallel with the cow’s backbone. Arm detachers need to be properly maintained with tight joints so that the unit stays in its set position. Parallel parlors require a unit adjustment support that can slide on the curb and move easily up and down to compensate for various udder heights.
Liner Type and Condition. Liner design usually has a greater effect on milking characteristics than any other machine factor. Machine-induced congestion and edema is reduced by milking with a "narrow-bore" liner having a soft mouthpiece lip. Swelling of the liner barrel usually results in increased strip yields and higher somatic cell counts in subclinically infected quarters. Liners should be designed to fit the teatcup shells. Mouthpiece deterioration usually results in increased squawking and liner slips. The mouthpiece should not be distorted by the shell but should be held firmly enough not to twist easily in the shell. Teatcup shells should all be the same length. Liners should have no cracks in the short milk tube connecting to the claw. If there is a significant change in milkability when liners are replaced, liners were used for too many cow milkings.
Cluster Air Admission. Blocked or partially blocked air vents reduce claw vacuum level, increase claw vacuum fluctuations, increase cluster flooding and liner slip, and increase milking time per cow. Vents should be in either the claw or teatcup liner but not both. Excessive air admission tends to reduce claw vacuum level and increase claw vacuum fluctuations and tends to cause more milk frothing and lipolysis which may contribute to lower milk quality Vents should be checked at every milking to make sure that they are clean.
Completeness of Milking. If strip yields average more than 1 pound per cow, by hand-stripping at least 10 cows into a bucket, completeness of milking is a problem. Strip yields should be less than 0.5 pound per cow. The most common causes of poor milkout are: poor type or condition of liner; mismatch between claw inlet and short milk tube; clusters too light; clusters that do not hang evenly on the udder because connecting hoses are too long, too short, twisted, or poorly aligned; or high milking vacuum levels.
Milking System Performance Analysis
In maintaining or trouble-shooting milking equipment, the following components or tests are important in order to minimize or eliminate the concerns or problems that were discussed above. Milking system tests should be conducted on a regular basis by a trained serviceman using procedures outlined by the National Mastitis Council. These tests should include:Operating vacuum level- Compare test gauge vacuum to system gauge, usually done with an air flow meter;
Vacuum pump capacity- Measured with an air flow meter at 15 inch vacuum to determine if vacuum pump delivers rated capacity;
System leakage- Conducted with an air flow meter at the receiver (or a test port) with regulator closed or removed, pulsation disconnected, and adjusted to 15 inch vacuum. The difference between this reading and pump capacity indicates vacuum lost through leaks or pipe restrictions;
System reserve and unit consumption- Repeat system leakage test but conduct with pulsators connected and milking units under vacuum and teatcups plugged with artificial teats if possible;
Manual reserve- Repeat system reserve determination but read cfm at 0.6 inches below vacuum setpoint.
Cluster fall-off requirement- Invert one milking unit for each 8-10 units on the system and open the unit vacuum shutoff valve to permit the maximum amount of air to be admitted to the system. Air flow should be measured at 15 inches. This is the amount of air required when one unit falls off. If the vacuum level does not reach 15 inches, the vacuum reserve is not adequate;
Regulator load test- Reconnect the regulator. Read the vacuum level when the air flow meter is completely closed. Open the air flow meter in 5-10 cubic feet/minute (cfm) increments and read the vacuum level. A good regulator sustains vacuum level within 0.6 inch of setpoint when 90% of the system reserve is admitted. If the vacuum drops 0.6 to 1.0 inch at 90% of reserve, the regulator is marginal. If the vacuum drops more than 1 inch, the regulator is either dirty or needs repair or replacement.
Effective reserve- Using the air flow meter at the receiver and the regulator reconnected, the effective reserve is the cfm reading at 0.6 inch below the vacuum setpoint which should provide an operator reserve of at least 35 cfm (or cluster fall-off, whichever is greater) + 0.7 times the number of units. For a double 10 parlor, 0.7*20 units equals 14 + 35 operator reserve equals an effective reserve of 49 cfm (American standard).
Regulator loss- Compare the manual reserve to the effective reserve. The difference is cfm lost through the regulator which should not exceed 10% of manual reserve.
Regulator response- This test assumes that the system is adequate to handle a falloff. Invert one unit for each 8-10 units and open the unit vacuum shutoff. An adequate system with a good regulator will hold the vacuum drop to 0.6 inch or less. Quickly close the vacuum shutoff. The regulator should not allow the vacuum level to overshoot the vacuum setpoint by more than 0.25 inch. This last test can be conducted by farm staff and should be done weekly.
Individual pulsators should be graphed at least every 6 months to determine if they function properly. Pulsators should be cleaned and rubber parts replaced according to a schedule of machine use, but at least every six months. Only 25% of Florida dairies had all pulsators working properly when visited (Bray et al., 1998).
Vacuum levels and regulation. Sensitive regulators should be installed in clean, dry, dust-free, and convenient locations, either off the distribution tank or the main airline as near the sanitary trap as possible (ASAE, 1996). They should be cleaned at least monthly (twice a month is preferred) and filters changed as needed. Vacuum level and fluctuation at the teat end should be checked. An adequately designed milking system with proper vacuum pump capacity and low milk lines or weigh jars should have a vacuum level of 11-13 inches at the teat end at peak milk flow with no more than 2-3 inch" fluctuation during several pulsation cycles.
Teatcup liners should be replaced according to manufacturer's recommendations. When liners were used excessively, bulk tank milk in 10 Ohio herds over 52 consecutive weeks had higher bacteria counts, especially Staphylococci (Hogan et al., 1988). Teatcup liners, when not sanitized after milking infected cows, may transfer infections to uninfected cows and cause new mastitis infections. Mastitis infected cows should be milked last or into separate milker units used only for infected cows. Studies at Virginia Tech have found that sanitizing units after milking infected cows is another effective control measure that reduces incidence of new infections (Grove and Jones, 1992). The use of automatic teat cup backflushing is another alternative that may be cost effective. Of special concern is the milking of first lactation cows after milking infected cows; milk clean, uninfected cows first.
Other milking system components that should be changed every 3-4 months include: milk hoses, short air tubes, gaskets, and rubber plugs.
Pulsation lines should be cleaned on a regular basis as condensation, milk droplets and airborne contaminants are frequently drawn into vacuum lines (as well as milk from split teatcup liners). Clean vacuum lines help to maintain optimum airflow within the milking system. A standard pipeline cleaner used monthly is adequate. Vacuum lines should be looped with valves and tees provided for slug washing of the vacuum line. Vacuum lines need to be sloped to drain. All low spots should have automatic drain valves and clean-out plugs.
Stray voltage. In recent years it has become evident that small electrical currents may come in contact with dairy cows and may cause significant behavior problems, accompanied by losses in milk production and certain health problems. If the voltage during milking exceeds 0.5 volts when measured at the barn service entrance ground or at various cow contact points (stalls, feeders, waterers, milk pipeline), a more detailed analysis should be conducted to isolate the source and determine whether it is on-farm (milk tank compressor, water heater, silo unloader, lights, electric fence, house, telephone, etc.) or off-farm (power line). For additional details, see Virginia Cooperative Extension Publication 404-250, Stray electricity on dairy farms (1992).
Milking system evaluation should be conducted at regularly scheduled intervals by a trained service representative. This evaluation should include:
- Vacuum pump
- System leakage
- Regulator performance
- Vacuum level and vacuum gauge
- Pulsator performance
- Air vents
- Condition of rubber and plastic parts
- Cleanliness
- CIP system function
- Stray voltage
Preventive Machine Maintenance
Milking machines are used 5-6 or more hours every day. Broken-down machines or machines operating inefficiently cost in reduced milk, time, damaged udders, and reduced milk quality. Regular service inspection will allow performance at high efficiency. There are certain maintenance checks that should be performed by the operator at every milking, and every 50 and 250 hours.Daily:
Weekly:
4-6 Weeks:
Every 6 Months:
References
American Society of Agricultural Engineers. 1996. Milking machine installations-construction and performance standards, ASAE S518.2 JUL96.
Bray, D.R., P.A. Fowler, F.B. Fialho, R.A. Bucklin, S. Yeralan, T. Tran, and R.K. Braun. 1998. An automated system for monitoring milking system parameters. Pages 127-136 in Proc. 37th Annual Meeting National Mastitis Council, Madison, WI.
Grove, T.M and G.M. Jones. 1992. Use of an enzyme-linked immunosorbent assay to monitor the control of Staphylococcus aureus mastitis. J. Dairy Sci. 75:423-434.
Hogan, J.S., K.L. Smith, K.H. Hoblet, P.S. Schoenberger, D.A. Todhunter, W.D. Hueston, D.E. Pritchard, G.L. Bowman, L.G. Heider, B.L. Brockett, and H.R. Conrad. 1988. Bacterial and somatic cell counts in bulk tank milk from nine well managed herds. J. Food Protection 51:930.
Mein, G. and D.A. Reid. 1996. Milking-time tests and guidelines for milking units. Pages 235-244 in Proceedings 35th Annual Meeting, National Mastitis Council, Madison, WI.
National Mastitis Council. 1996. Current Concepts of Bovine Mastitis, 4th ed., Madison, WI.
Rasmussen, M. D., E. S. Frimer, and E. L. Decker. 1994. Reverse pressure gradients across the teat canal related to machine milking. J. Dairy Sci. 77:984-993.
Stewart, S., R. Farnsworth, G. Mein, D.A. Reid, A.P. Johnson, G. Beehler, and J. Paasch. 1996. Field measurement of vacuum levels using a portable liquid flow simulator. Pages 214-227 in Proceedings 35th Annual Meeting, National Mastitis Council, Madison, WI.
March 1999